Since 2010, NCC BCA Section J Deemed-To-Satisfy requirements for limiting the power used by HVAC fan and pump motors has resulted in an increase to system duct and pipe sizes. At the same time, Section J has also increased minimum insulation R values and has moved to a “Material R value” basis for insulation systems, leading to increased thicknesses for traditional materials.
Although increasing the energy efficiency of building services systems is an essential action to control building-related energy use, the combined effect of these three changes has led to an increase in the spatial requirements of the services that need to fit into the plant rooms, shafts and ceiling spaces of BCA Deemed-To-Satisfy compliant buildings. In this “view from all sides” article, Vince Aherne, M.AIRAH, speaks to four experts about how the construction industry is dealing with these spatial issues.
Ever since humans first started erecting buildings, there has been conflict around providing space for building services. In days past this might have involved allowing space for tall ceilings to facilitate ventilation and comfort, or inserting large, high windows for adequate day lighting.
In many contemporary buildings the indoor environmental conditions are provided by building services systems, which all need to be accommodated within the often-hidden building spaces of plant rooms, shafts, false ceilings and raised floor spaces.
Smash the myth: GREEN HVAC is not lean HVAC
“There is a myth pervading the industry that being green means being lean, and that energy-efficient HVAC systems are somehow smaller than standard systems,” says Scott Brown, M.AIRAH, sustainability director with Waterman Group.
The truth is that while a green building might reduce dependency on HVAC, all things being equal, Brown says that energy-efficient HVAC systems are more likely to lead to an increase in spatial requirements, not a decrease.
He says bigger ducts with more insulation need bigger shafts and deeper ceiling spaces. More efficient chillers and boilers need bigger heat exchangers, with more plantroom access.
“A greener system configuration with air-to-air energy recovery, for instance, means more ductwork and additional heat exchangers to fit in,” Brown says.
Brown notes that plant rooms with energy-efficient HVAC plant and air-to-air heat recovery can be 50 per cent or even 100 per cent bigger than they would have been had energy efficiency not been a concern.
Mark Lee, Affil. AIRAH, is engineering manager with mechanical contractor James L Williams. He says that generally speaking, building designers allocate the same or smaller spaces for building services as they have in the past, making access tight and providing for future maintainability very difficult.
So the same old battles are being fought by designers.
“It is not the cost of larger ducts or plant that is the issue,” says Lee. “It is the cost of the additional space required that seems to be the limiting factor.”
Space, in other words, is the crunch point.
The race for space
Jason Veale, associate director – building engineering with AECOM, agrees.
“Every project has a degree of tension between architects and engineers over spaces,” he says. “Section J is now increasing the need to coordinate and communicate about service space early.”
According to Peter Cass, M.AIRAH, who is associate – services cost management with Rider Levett Bucknall, architects are pivotal to changing space allowances because they own the building spaces.
But as Cass explains, extra space is not always a straightforward proposition.
“Developers are measuring new projects against the space ratios of the existing buildings that will compete for the same tenants,” Cass says.
Cass says that to some developers, any non-lettable space is viewed as wasted.
Brown, Cass and Lee all agree the reality is that allocating additional space is very expensive. Construction costs will change, which affects the profitability of an entire project.
“There may be occasions when bigger shafts might be accommodated,” says Veale. “But deeper ceiling spaces? No way.”
So, all agree that there has been no apparent change in spatial allowances for services, and that building floor-to-floor heights have not changed.
“The reality is that, in most cases, larger services are being squeezed into the same or smaller spaces to the point that coordination is almost impossible,” Lee says.
Although new tools such as BIM software and visualisation or clash-detection tools can predict and highlight clashes between services, it is the practicalities around the space needed for installation that is a key pressure point on site.
“The pressures exerted by architects, designers and builders mean that on site, it becomes a race to install your services first so that the other trades have to work around you,” Lee says.
Though 3D building models are useful tools for laying out services, they do not solve all the issues around access for installation.
Old solutions can no longer be applied
Lack of services space has always been a barrier to optimum performance. In the past, when a clash with existing services or immovable structural component was encountered, distribution systems could be made to work, by flattening ductwork or installing aerodynamically restrictive bends.
Some of these transitions are quite extreme, and these types of “solutions” reduce system energy efficiency. In fact, they are exactly the type of thing that the NCC Section J rules are attempting to address.
As Veale says, duct routes are often chosen with little regard to the impact on overall fan energy. Restrictions at the inlet and outlets of fans and air-handling units can significantly degrade the expected system performance. The motor power and energy consumed rises as the resistance along the distribution route goes up. Now these make-it-work options are no longer available due to overall power restrictions, so what is an industry to do?
What are the solutions?
Apart from providing additional space for services accommodation, there are a few alternative options available.
“The market is always keen to respond, and some HVAC solutions have different spatial requirements than others,” Cass says.
Brown notes that chilled beam systems tend to be more space efficient, and can be left exposed if aesthetically desirable.
Cass agrees, and notes that distributed systems – for example, many smaller systems rather that single, large central systems – and underfloor air distribution systems, are also becoming popular, for a variety of reasons, including space considerations.
Cass also says chilled and/or heated structures (floors, walls, ceilings) are another option that is being adopted to keep ahead of the curve for building design.
However, as Brown points out, these solutions themselves tend to have a significant cost premium over the more standard HVAC methods, and this all needs to be added into the mix. Also, these solutions, if not correctly and appropriately implemented, can lead to issues with indoor air quality, condensation and mould.
All our experts agree that new attitudes regarding energy efficiency must be developed by architects, developers, and by the eventual building owners and tenants.
“Building designers and developers are well aware of the benefits of energy-efficient services systems,” Lee says. “Those benefits generally flow to the occupier, who is often not the building owner, nor the entity paying the construction costs”.
So the same old split-incentive barriers apply.
Asks Cass: “Why should a developer or building owner pay additional construction costs to reduce operating costs for future tenants?”
Green leases go some way to addressing this, as do building rating systems that can be used to market a building for sale or lease.
“Engineers need to push harder and sell the merits of increased services space to designers and builders,” Cass says.
“Green Star and NABERS do a great job of recognising buildings designed with improved energy efficiency,” says Cass, adding that this includes HVAC systems that have larger ducts and pipes.
Eventually end users will drive this agenda when they begin to favour (that is to say, pay more for) energy-efficient building spaces.
In addition, as Lee points out, there are many other benefits of increased or reasonable services space, including less wastage and rework on site due to services clashes, faster installation time, reduced installation costs, and better access for maintenance and inspection for the life of a system. These benefits also need to be recognised.
Alternative solutions; life is a trade-off
“It is becoming increasingly common now for designers to use the alternative JV3 modelling approach to reduce insulation requirements for pipes and ducts to avoid increases in ceiling depths,” Veale says.
JV3 modelling allows trade-offs between system components because it is the overall performance of the system that is assessed.
“Over-complying on performance for chillers, pumps, fans and lighting can allow for a relaxation of insulation requirements and still produce an equivalent overall energy result,” Veale says.
A bigger chiller in the plant room might allow a smaller duct on the occupied floors, for instance.
“If spaces are going to be squeezed to the extent that it affects the profitability of the project then JV3 is used to avoid that situation,” Veale says.
“JV3 modelling almost always improves the situation significantly, and the modelling and design work comes at a fraction of the cost of losing a floor off the top of a building.”
How can the awareness of these issues be raised within the industry?
One suggestion from Lee about how awareness can be raised is the introduction into the NCC of minimum aspect ratios for ducts, or a standard calculator, like that used for glazing. This would help consultants and contractors prove to builders that a system will not comply if it is forced into the restrictive spaces they propose.
Says Brown: “Education and awareness building is the key. The myth that green always means lean for HVAC systems needs to be broken.”
A suggestion from Veale is for engineers to document the final insulated dimensions of the ductwork, and not the sheet metal dimensions. Design drawings often show sheet metal sizes for pricing; construction drawings often show sheet metal sizes for fabrication. Yet these metal sizes are generally not the final spatial size required if the duct is to be externally insulated.
All agree that the design team needs to establish the spatial requirements very early in the process so it can be accommodated, and make sure all stakeholders know why it is occurring.
“A good design team will have a workshop to deal with it,” says Veale.
Communications around spatial requirements need to be ongoing as the project progresses.
Is better integration in the design process the key?
“The balance of benefits and costs does not appear to have been addressed holistically within building regulations,” Brown says. “A lot of attention has been given to the final energy efficiency of HVAC plant, but little given to the additional space, materials and embodied energy required to implement such plant.”
Given the imperative to reduce the energy consumption of buildings, it is surprising that building services – one of the major components of energy usage and cost – are rarely considered in the early stage of a design or as potential driving factors for form and spatial configuration.
It is the building orientation, form and fabric aspects that generally dominate the cooling and heating loads. In order for the form and geometry of buildings to be considered in response to energy efficiency and building services optimisation, multidisciplinary integration is required in the early stages of the design process, when the design proposal is still flexible.
So, to sum up, energy-efficient HVAC tends to be bigger than standard HVAC. Energy-efficient and green buildings tend to provide the same or less space for services than standard buildings. Something has got to give. Engineers push for more space, and architects and developers push back or resist.
The final answer is somewhere in between, after both engineer and architect have pushed to be as efficient in their spatial requirements as possible.
JV3 energy modelling offers an alternative compliance path for those buildings and systems that encounter significant problems with NCC-driven Deemed-To-Satisfy pipe and duct sizes.
AIRAH would like to thank the following individuals for sharing their views in this article with Vince Aherne, M.AIRAH:
Scott Brown, M.AIRAH, sustainability director – Waterman Group
Peter Cass, M.AIRAH, associate, services cost management – Rider Levett Bucknall
Mark Lee, Affil.AIRAH, engineering manager – James L Williams
Jason Veale, associate director, building engineering – AECOM.
Image Below: Supplied
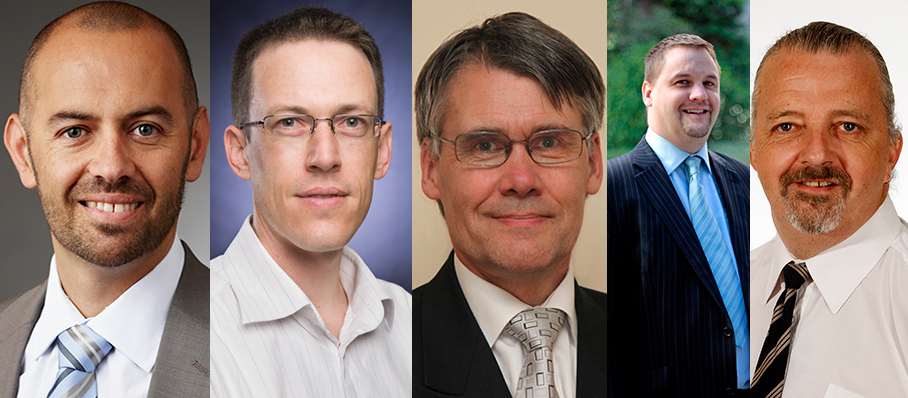